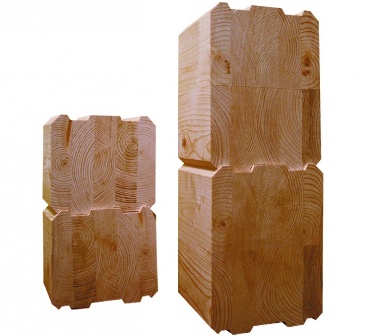
Дома из брёвен строят по всему миру в течение тысяч лет. В наше время технология строительства таких домов стремится к совершенству. Помимо того, что дерево обладает превосходными строительно-техническими свойствами, с ним связаны простые жизненные ценности, касающиеся качества человеческого существования. В деревянном доме человеку легко дышится и уютно живётся. Красивое, светлое дерево положительно влияет на настроение. Древесина также является таким строительным материалом, который не загрязняет окружающую среду и не мешает природе обновляться.
В отличие от остальных строительных материалов дерево «дышит». В клеточном строении бревна незаметно происходит постоянный обмен воздуха. Одновременно, влажность воздуха внутри дома поддерживается на оптимальном для человеческой жизни уровне сама собой, без специального оборудования для кондиционирования воздуха. По сравнению с кирпичными и бетонными стенами той же толщины, бревенчатая стена имеет в несколько раз лучшую теплоизолирующую способность.
Основой современной технологии строительства деревянных домов, как и прежде, остаётся сосновое, или еловое бревно. Хвойные породы являются самыми подходящими для строительства бревенчатых домов благодаря своему прямому строению и хорошей воздухопроницаемости. Но для того, чтобы положить его в сруб дома, отвечающего требованиям сегодняшнего заказчика, оно должно несколько видоизмениться.
Сегодня строят дома из профилированного бревна или клееного бруса.Первая стадия обработки бревна проста – это либо распиловка его в брус, либо окорка и грубая оцилиндровка. Затем производится «пикировка» - тонкий пропил по всей длине бревна, достигающий его сердцевины. Эта операция необходима для того, чтобы внутренние напряжения, неизбежно возникающие на стадии сушки, не рвали дерево на трещины «где попало». Трещина пойдёт вдоль пропила, и, при дальнейшем профилировании, она будет расположена на нижней части бревна.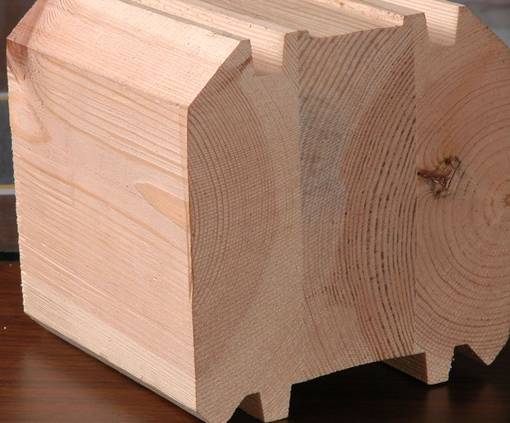
После сушки до 18-20 процентов влажности оцилиндрованное бревно или брус подвергаются четырёхсторонней обработке для получения необходимого профиля. После торцовки и/или нарезки на нужную длину брёвна или брусья поступают на станок для зарезания «лап» или профилирования замков более сложной формы После этого, комплект дома упаковывается и его можно отправлять на стройплощадку вместе с другими необходимыми компонентами. |
Однако, и такие дома подвержены усадке, что доставляет определённые неудобства: либо заказчику приходится ждать около года, прежде, чем приступить к окончательной отделке, либо производителю вкладывать дополнительные средства в организацию склада естественной сушки материала.
Теперь мы рассмотрим то, как лучше организовать производство клееного бруса. Вот основные технологические этапы, необходимые для изготовления продукции мирового уровня качества:
- Распиловка бревна (ленточное или дисковое лесопильное оборудование);
- Сушка древесины (сушильная камера);
- Калибровка (рейсмус);
- Раскрой по ширине для вскрытия дефектов (многопильный станок);
- Выборка дефектов (торцовочный станок);
- Склеивание ламели по длине (линия торцевого сращивания);
- Калибровка ламели (четырёхсторонний фрезерно-калёвочный станок);
- Склейка ламелей на гладкую фугу (гидравлический пресс);
- Профилирование бруса (четырёхсторонний фрезерно-калёвочный станок);
- Торцовка бруса в размер (торцовочный станок);
- Зарезание чашек (чашкорезный станок);
- Засверливание отверстий под нагели (сверлильный станок).
На первый взгляд эта технологическая цепочка может показаться весьма трудоёмкой, однако её конечный продукт обладаетнеоспоримыми преимуществами.
Полученный материал обладает высокими технологическими и эстетическими свойствами: благодаря снятию внутренних напряжений такой брус не «ведёт», это материал, не подверженный усадке (в отличие от обычного бревна или бруса), который можно собирать на площадке, как конструктор, и сразу же вставлять окна, двери, устанавливать внутренние перегородки и приступать к отделке. Можно изготавливать цельные конструкционные детали нестандартной длины (т.е. более 6 метров). |
![]() |
Кроме того, более качественный материал («ангарскую» безсучковую сосну, например), можно пускать только на наружные слои, а внутренние изготавливать из менее ценного. Для стенового бруса можно даже срастить дефектные участки ламелей и чередовать их с обычными во внутренних слоях клееного бруса.
Такое производство в минимально допустимом с экономической точки зрения варианте может занимать площадь в 1000 кв.м., потребляя 300-400 Квт электроэнергии. Специальных фундаментов под станки не требуется – достаточно стандартного ровного бетонного пола толщиной 30 см. На нём может быть занято 15-20 рабочих. Если оснастить его бойлером на древесных отходах, получится производство полного цикла: тепла хватит и на обогрев цеха, и на поддержание работы сушильных камер.
На приобретение полного комплекта оборудования придётся затратить около пятисот тысяч долларов США. Если же такая цифра не по карману, можно комплектовать его поэтапно: закупать не брёвна, а доски, и начать с позиций 2, 5, 9 и 11 (потратив на их приобретение чуть больше ста тысяч долларов), на которых можно производить качественный профилированный брус и строительный погонаж и постепенно, с ростом получаемой прибыли, доукомплектовывать его позициями 3, 4, 6 и 8, что позволит изготавливать клеёный брус. А затем увеличить мощность сушильных камер, поставить участок распиловки, что позволит снизить расходы на закупаемое сырьё, добавить сверлильный станок и связать всю технологическую цепочку системой транспортировки – и вывести таким образом производство на полную мощность. Если добавить горизонтальный пресс и двусторонний шипорезный станок, на этом же производстве можно будет изготавливать мебельный щит, паркет и оконную заготовку, а добавив угловой центр вы сможете изготавливать и окна – то есть всё, что практически необходимо для строительства коттеджа полностью.
Некоторые, правда, начинали своё производство всего лишь с одного четырёхстороннего фрезерно-калёвочного станка ($ 42 000)