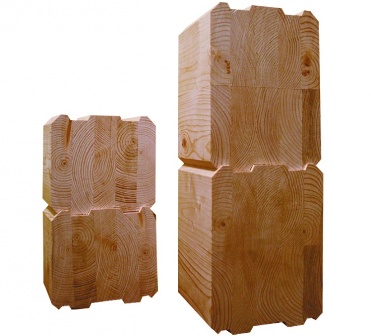
Основою сучасної технології будівництва дерев'яних будинків, як і раніше, залишається соснова, або ялинова колода. Хвойні породи є найбільш підходящими для будівництва дерев'яних будинків завдяки своєю прямою будовою і хорошою повітропроникністю. Але для того, щоб покласти його в зруб будинку, що відповідає вимогам сьогоднішнього замовника, воно має дещо видозмінитися.
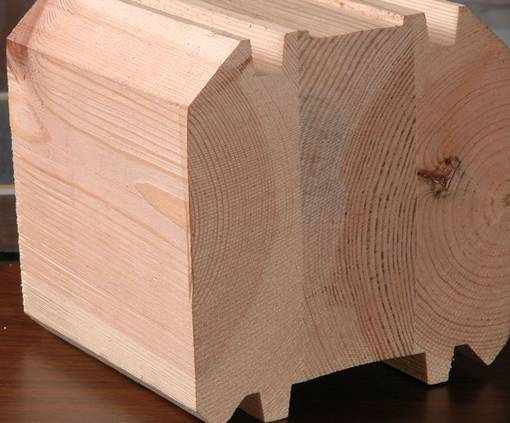
Сьогодні будують будинки з профільованого колоди або клеєного бруса.
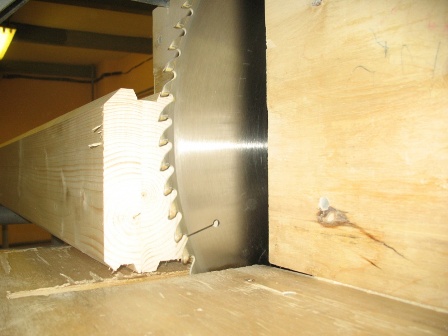
Однак, і такі будинки схильні до усадки, що має певні незручності: або замовнику доводиться чекати близько року, перш, ніж приступити до остаточної обробки, або виробникові вкладати додаткові кошти в організацію складу природної сушки матеріалу.
Тепер ми розглянемо те, як краще організувати виробництво клеєного бруса. Ось основні технологічні етапи, необхідні для виготовлення продукції світового рівня якості:
- Розпилювання колоди (стрічкове або дискове лісопильне обладнання);
- Сушіння деревини (сушильна камера);
- Калібрування (рейсмус);
- Розкрій по ширині для розтину дефектів (багатопильний верстат);
- Вибірка дефектів (торцювальний верстат);
- Склеювання ламелей по довжині (лінія торцевого зрощування);
- Калібрування ламелей (чотиристоронній фрезерно-клеючий верстат);
- Склеювання ламелей на гладку фугу (гідравлічний прес);
- Профілювання бруса (чотиристоронній фрезерно-клеючий верстат);
- Торцювання бруса в розмір (торцювальний верстат);
- Заріз чашок (чашкорізний верстат);
- Засвердлювання отворів під нагелі (свердлильний верстат).
На перший погляд цей технологічний ланцюжок може здатися вельми трудомістким, однак його кінцевий продукт володіє суттєвими перевагами.
Крім того, більш якісний матеріал («ангарська» безсучкова сосна, наприклад), можна пускати тільки на зовнішні шари, а внутрішні виготовляти з менш цінного. Для стінового бруса можна навіть зростити дефектні ділянки ламелей і чергувати їх із звичайними у внутрішніх шарах клеєного бруса.
Таке виробництво в мінімально допустимому з економічної точки зору варіанті може займати площу в 1000 кв.м., споживаючи 300-400 Квт електроенергії. Спеціальних фундаментів під верстати не потрібно - достатньо стандартного рівного бетонної підлоги товщиною 30 см. На ньому може бути зайнято 15-20 робітників. Якщо оснастити його бойлером на деревних відходах, вийде виробництво повного циклу: тепла вистачить і на обігрів цеху, і на підтримку роботи сушильних камер.
На придбання повного комплекту обладнання доведеться затратити близько п'ятисот тисяч доларів США. Якщо ж така цифра не по кишені, можна комплектувати його поетапно: закуповувати не колоди, а дошки, і почати з позицій 2, 5, 9 та 11 (витративши на їх придбання трохи більше ста тисяч доларів), на яких можна виробляти якісний профільований брус і будівельний погонаж і поступово, зі зростанням отримуваного прибутку, доукомплектовувати його позиціями 3, 4, 6 і 8, що дозволить виготовляти клеєний брус. А потім збільшити потужність сушильних камер, поставити ділянку розпилювання, що дозволить знизити витрати на сировину, додати свердлильний верстат і зв'язати весь технологічний ланцюжок системою транспортування - і вивести таким чином виробництво на повну потужність.
Якщо додати горизонтальний прес і двосторонній шипорізний верстат, на цьому ж виробництві можна буде виготовляти меблевий щит, паркет і віконну заготовку, а додавши кутовий центр ви зможете виготовляти і вікна - тобто все, що практично необхідно для будівництва котеджу повністю.
Деякі, правда, починали своє виробництво всього лише з одного чотиристороннього фрезерно-клеючого верстата ($ 42000)