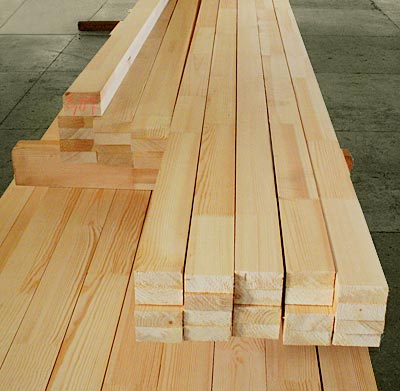
Растущий по понятным причинам спрос на окна из дерева в стране вызвал неминуемый рост количества производителей клеёного бруса, т.е. оконной заготовки. В общении с производителями окон, покупающими клеёную заготовку на стороне заметно, что они все, как один, столкнулись с проблемой контроля её качества и выбора надёжного, а главное – стабильного - поставщика. В связи с этим интересно посмотреть, как с этой проблемой справляются наши зарубежные коллеги. Эта статья из итальянского журнала "Xylon" поможет хоть кому-нибудь не наступить на грабли, на которых уже многие побывали.
Всеми признан тот факт, что объём клеёной древесины, используемой для производства окон в Италии, постоянно возрастает.
Этот растущий спрос немедленно встретил встречное предложение в виде появления большого числа мелких и средних производителей клеёных заготовок, сразу же вступивших в эффективную конкуренцию на рынке. С одной стороны, этот факт можно расценить, как благоприятный – цены понизились. С другой стороны, все гарантии качества на конечный продукт были тем самым уничтожены.
Определение качества клеёной оконной заготовки в
Италии не основывается на каких-либо специфических стандартах или
правилах. Существует только один стандарт, а именно EN 204-D4, который
определяет качество клеевого соединения и, в силу отсутствия
альтернативных методов, может быть применён также к клеёной заготовке.
Правда, он послужил основой разрабатываемого в настоящее время
специального стандарта, копия которого сейчас ходит по различным
инстанциям, и который, возможно, скоро будет принят.Возвращаясь к EN 204-D4, единственному имеющемуся на
сегодняшний день нормативному документу в этой области, можно отметить
следующие его положения:
Общие требования: соединение должно выдерживать погодные условия, типичные для региона со средним климатом (климатическая зона «Т» по стандарту DIN 500019, часть 1), при жёстких условиях эксплуатации.
Область применения: как внутри, т. е. в помещениях, обладающих перепадами температур и высокой влажностью (бассейны, ванные комнаты и т.п.), так и снаружи (двери и окна, обработанные пропитками и лаками, лестницы и т. п.).
Протокол испытаний: как указано в стандарте, информация взята на основе древесины бука, высушенной до влажности 12+/-1%, а затем протестированной на силу адгезии по окончании каждой стадии процесса. Тест считается пройденным, если образец прошёл следующие минимальные испытания:
- 7-дневная выдержка в нормальной атмосфере, т.е. при температуре 23+/-2 градуса по Цельсию и относительной влажности воздуха 50+/-5%, или при температуре воздуха 20+/-2 градуса и относительной влажности 65+/-5%. После этого предел прочности на разрыв должен составлять не менее 10 Н/мм2.
- 7-дневная выдержка в нормальной атмосфере. 4-х дневная выдержка в холодной воде (при той же комнатной температуре). После этого предел прочности на разрыв должен составлять не менее 4 Н/мм2.
- 7-дневная выдержка в нормальной атмосфере, 6 дней в горячей воде, 2 часа в холодной воде. После этого предел прочности на разрыв должен составлять не менее 4 Н/мм2.
- 7-дневная выдержка в нормальной атмосфере. 6 дней в горячей воде, 2 часа в холодной воде и ещё 7 дней в нормальной атмосфере. После этого предел прочности на разрыв должен составлять не менее 8 Н/мм2.
При этом понимается, что, по практическим причинам, образцы подготавливаются в идеальных условиях, учитывая то, что окончательные результаты испытаний зависят от следующих факторов:
- свойства древесины (разные породы ведут себя по-разному и результаты их склеивания могут отличаться от тех, что заявлены производителями клея на основании испытаний тестовых образцов);
- влажность древесины (которая на стадии склеивания является критическим фактором для катализации клея и стабильности состояния конечного продукта;
- количество нанесённого клея (определяемого производителем клея либо вышеназванным стандартом; специального стандарта на этот предмет не существует);
- время прессования (производители клея указывают обычно слишком большое время, чтобы можно было его соблюдать в промышленных условиях. Обычно пользователи сами практическим образом находят подходящее время, и оно, как правило, бывает значительно меньше указанного);
- усилие прессования (само собой разумеется, что оно должно быть тщательно откалибровано, поскольку, как же говорилось, различные породы древесины ведут себя неодинаково);
- температура прессования (горячее прессование даёт ощутимые преимущества в смысле сокращения времени прессования, но нельзя сказать, что оно автоматически гарантирует более высокое качество продукции; начиная с толщин 30 мм и более единственный процесс, способный дать качественное склеивание, это – высокочастотный нагрев, так как только он нагревает клей, не влияя при этом существенно на влажность склеиваемых деталей);
- температура окружающей среды перепады температуры в рабочем помещении влияет на время, необходимое для качественного склеивания: чем ниже температура, тем длительнее оно должно быть;
- качество поверхностей (для грамотного соединения поверхности должны быть идеально плоскими; так же очевидно, что время между подготовкой поверхности и нанесением клея должно быть минимальным, поскольку естественное старение приводит к тому, что на поверхность выступают содержащиеся в древесине смолы, масла и минеральные субстанции, которые, вступая в химическую реакцию с клеем могут замедлить процесс, или привести к ослаблению соединения);
- условия хранения клея (производители клея всегда указывают условия его хранения, которые должны неукоснительно соблюдаться).
Благодаря всем вышеперечисленным переменным факторам, производство клеёных изделий требует регулярного контроля для того, чтобы поддерживать качество продукции на должном уровне.
Итальянские лаборатории, имеющие необходимое оборудование, пока ещё ни разу не проводили сертификацию полного цикла такого производства, за исключением редких испытаний отдельных образцов.
Надо сказать, что и сами производители не горят рвением проходить сертификационные испытания, так как соблюдение всех необходимых требований неизбежно приводит на первых порах к снижению производительности. Максимум, на что пошли некоторые крупные производители – это создание собственных подразделений контроля качества, однако, контролёр, который сам себя контролирует, знаете ли, не всегда приносит пользу.